1 前言
阀门定位器是调压阀的关键配件,其精度等级是全部调节阀门自动控制系统能不能精确完成的关键步骤。因此,研发好用、高效率的定位仪自动控制系统对工控自动化而言有着比较大现实意义,为减少项目成本、减少周期时间、便捷系统软件主要参数的改动,选用系统软件建效仿真的是一种不错的方式 。而智能化阀门定位器特性又关键受调整组织的危害,因此文中就以调整组织中的气动式薄膜调节阀为例子,融合手机定位系统其他各阶段元器件特点及工作状况特性,创建闸阀手机定位系统的动态性实体模型并开展科学研究。
2 调节阀门手机定位系统构造
如下图1所显示:执行器行程安排为30mm;机械结构较大拐角600度,通过减速比为2∶1的传动齿轮系,使电阻器较大转动1200度;电阻器在电源电压3.3V功效下导出0~1.1V电流电压数据信号,再通过3倍放大仪变换为0~3.3V阀位意见反馈数据信号;上位机软件导出设置行程安排0~0.03m,转换为0~3.3V电流电压数据信号,与反应数据信号较为导出误差数据信号,经PWM控制板解决后造成pwm占空比数据信号以操纵压电式阀的导通,完成电气设备变换;规范气动阀门(140~250KPa)根据压电式阀推动执行器姿势。
3 PWM操纵
压电式阀的调节数据信号选用PWM操纵,打开时长Ton在脉冲宽度周期Twm范畴内可变,pwm占空比D为二者之比,D在0~100%可变。操纵数据信号与导出pwm占空比D的联系如下所示:
当部位误差e比较大时,则导出持续数据信号给压电式阀(迅速调整);当部位误差e大小适度,则导出矩形脉冲给压电式阀(慢速度调整);当部位误差在制定的不大范畴0.1%(过流保护)内时,觉得电动执行器抵达制定部位,这时关掉调节阀门,使电动执行器精准定位在所在位置。
4 系统软件实体模型
(1)压电式阀总流量方程式
本系統选用PWM方法对压电式阀开展操纵,回应工作频率较高,可以忽视在开启和关上时时长上的落后,其宏观经济实际效果(时长均值)等同于更改导向性阀的张口总面积,促使切断阀PWM信号操纵时,其导出具备比例阀的特点。忽视压电式阀的信息特点,通常采取的是Sanville流量公式计算,将根据阀门的空气流动性全过程类似为理想气体根据收拢喷嘴的一维等熵流动性。
针对调整进气口和排气管的2个压电式阀,当PWMpwm占空比为D时,阀的合理总面积可以表述为:S=S0•D,压电式阀门流量系数为Cv,故总流量方程式表明为:
气动阀门的压力为P1,相对密度ρ1,流动速度为v0≈0,环境温度为T0,喷嘴出入口工作压力P2,汽体流动速度v,相对密度ρ2,环境温度为T2,出入口总面积为S0,汽室工作压力pb。
当出入口工作压力小于气动阀门工作压力时,阀对汽缸开展打气,压电式阀的进风口工作压力P1为参量,阀的总流量仅是阀心的偏移量和排气口工作压力的函数公式,方程式在平衡位置的情形下开展归一化处理得:
令压电式阀均衡工作中点总流量增益值,均衡工作中点总流量工作压力指数;则:
试验认证取压电式阀门流量系数Cv=0.68较有效。
打气情况(气动阀门≥140kpa)汽体流动性为亚音速流动:
排气管情况(空气≤100kpa)汽体流动性为音速流动:
(2)气动执行器实体模型
气动执行器膜头可以转化为标准气压变换阶段、力变换阶段和偏移变换阶段。
标准气压变换阶段可类似为阻容阶段解决:键入标准气压数据信号变换为膜头内标准气压,其静态数据特性即增益值为1,因而在供气管道和制动气室不泄漏时,该阶段的输入输出数据信号在稳定时与键入数据信号应一致,开环传递函数为:
充分考虑具体工作中,气动式管道有一定摩擦阻力外,也有其惯性力和容积,因而开环传递函数可简化为:
力变换阶段类似做为线形占比阶段解决:膜头内标准气压变换为推动力,静态数据特性由塑料薄膜合理总面积决策,开环传递函数Ft(s)=Aep2(S)。
具体工作中,塑料薄膜片的合理总面积产生细微转变,推动力也会出现细微转变,导致左右行程安排时的回差及一样标准气压下推动力的误差等,进而引进最优控制。
偏移变换阶段是将推动力摆脱阀的不平衡感和滑动摩擦力等产生的协力变换为偏移,具体工作中,因为该阶段有滚动摩擦力,工作温度转变使刚度系数产生变化使之变成最优控制阶段,运用中只有类似为线形阶段解决,开环传递函数:
因而气动式塑料薄膜执行器开环传递函数可类似为:
具体运行状态下,TV1并不是线形的,刚度系数和膜头合理总面积会产生变化,因而,执行器静态数据特点系统对的危害主要表现为最优控制。气动仪表实质上属于非线性系统,但归一化处理剖析为系统软件信息特点定性研究给予了一种合理的方式,与此同时假设动态性流程中各参数的改变仅是一个细微量(小振荡),进而为系统软件实体模型的分析带来了便捷。
♂
5 仿真实验剖析
(1)系统软件性能指标
为检测所创建动态性自动控制系统实体模型的特性,在系统软件响应时间和动态性实验数据层面,各自选用阶跃数据信号和正弦函数数据信号开展追踪仿真实验,试验结论基本上完成自动控制系统规定。如下图2、3所显示。
(2)总流量特点模拟仿真
当调节阀门与管路串连时,调节阀门总流量特点即是串连管路工作中总流量特点,其关键受力降的危害,压力降比S,为调节阀门全开时阀两边压力降与系统软件总压力降之比。当以管路压力降为零时的调节阀门开全总流量Qmax为标准时,调节阀门运作时最大的总流量减少,S越小失真越比较严重,较大数据流量的下降越大,其工作中总流量特点失真如下图4所显示:
当调节阀门与管路并接时,调节阀门总流量特点即是并接管路工作中总流量特点,其关键受商品流通总流量的危害,y为调节阀门全开时总流量与主管较大总流量之比,y越小,表明旁通总流量越大,则调节阀门工作中总流量特点越差。不一样的y值下,并接管路工作中总流量特点失真如下图5所显示。
(3)自动控制系统其他关键影响要素
气动阀门工作压力同样情况下,气动阀门工作压力在转变范畴内由小增加时,模拟仿真曲线图增益值和调整时长都减少,但造成超调增大PWM周期时间取样周期Tpwm过交流会可能会导致不稳定;Tpwm过小,工作频率很高,会扩大超调合调整时长与此同时减少执行器使用期限,因此单脉冲周期时间的设定应当充分考虑其尺寸对控制系统性能参数的危害,在容许的情形下,Tpwm的数据应尽量避免的大一些,运用中应使它与被测目标稳态值的比率在一个适合范畴内。
6 结语
文中构建的系统软件动态性实体模型选用了最优控制阶段类似解决,而具体之中各主要参数转变产生的影响要素,会在一定水平上危害系统软件可靠性,但模拟仿真实验结果显示,所确立的数学分析模型在PWM控制系统下,自动控制系统特性不错反映,可以做到具体使用的目地。
咨询需求
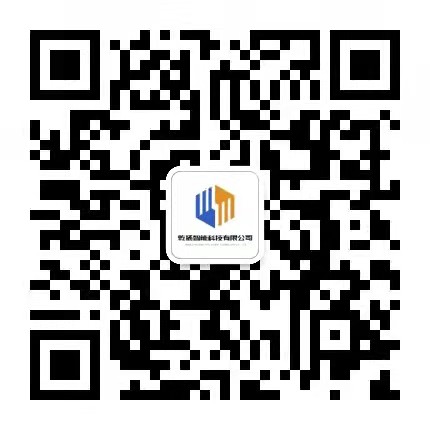