电动蝶阀的导出难以用一个精确的模型设计来叙述,但可以精确地精确测量。对于这一特性,步进式操纵不可以直接对输进数据信号开展回应,反而是分多个固定不动的步幅,依据每一次的测定结论使键入命令数据信号一步一步地靠近设定量分析。根据有效的操纵基本参数,该方式 使操纵目标运作稳定,适用对响应时间规定较低的总流量或负担的追随或平稳操纵。
电动蝶阀通常做为控制系统的一个构成部分,被用于对空气的总流量或工作压力开展调整。可是电动蝶阀的插入和导出相互关系难以用一个精确的模型设计来叙述。这不但是因为闸阀频率特性的最优控制,而其因为穿过闸阀汽体的数据流量和闸阀前后左右的压力降相互之间危害无法测算。以流量监控为例子,当闸阀前后左右工作压力固定不动时总流量仅与闸阀的开启度相关,但在大部分情形下,当闸阀的阀位转变时,闸阀前后左右工作压力也会随着转变,这就时总流量增益值的测算十分困难。实际上,因为闸阀前后左右的负担在振荡要素的效果下也会出现起伏进而造成总流量的转变,穿过闸阀汽体的用户流量与闸阀的开启度不会有一一对应的关联。因为数学分析模型的不确定性,立即以多孔板的开启度做为控制自变量不可以有效地达到系統的规定,乃至将会致使安全事故的产生。随后虽然闸阀的开启度与总流量或压力降中间的分析关联不容易获得,可是依靠检测仪表却可以便捷地对闸阀在某一开度下的总流量或压力降开展精确测量。
对于气动阀门的导出易精确测量不适合估算的特性,步进式操纵不可以直接对输进数据信号开展回应,反而是分多个固定不动的步幅,使键入数据信号一步一步地靠近设定量分析。在多孔板旋转一个步幅以后都对阀体的总流量或压力降开展一次精确测量,操纵电子计算机依据精确测量值和额定值较为的结论,明确下一步多孔板旋转的方位,直到精确测量值与额定值的误差低于要求偏差时才行。 步进式操纵的编程设计不涉及到数学分析模型的研究和求得,因此相对性非常简单,一般用plc梯形图就可以完成。编程设计框架图见图1。在编程设计中必须设置2个主要参数,及步幅和取样周期时间。这两个主要参数对自动控制系统的精密度和响应时间危害比较大,设置时要充分考虑对系统精度和响应时间的规定。
电动执行器可简化为由继电器阶段和开环传递函数两部份组合而成的自动控制系统,如下图2所显示。这一自动控制系统是以工作电压数据信号 Us(即 I/V 变换后的数据信号)为键入,部位反应数据信号 Uf 为导出。只需 |e|>h,交流伺服电机便会获得尺寸为 Ua 的配电工作电压。这时的前向开环传递函数为:
式中,m为 |e|>h 逐渐的时时刻刻,n为 |e|>h 完毕的时时刻刻。
对式(1)开展拉氏反转换,可以获得部位反应数据信号 Uf,即多孔板部位的变化趋势为:
当步幅比较大,一个步幅所历经的時间较长时,式中的最优控制项 e-(t-m) 和 e-(t-n) 对响应时间的干扰较小。相反最优控制要素对响应时间的危害比较大。不难看出,步幅越小,精度越高,但响应时间变慢。步幅的设置可以在操作系统的校准历程中依据对调节目标的测定结论开展,多孔板旋转一个步幅所造成的总流量或压力降的较大变化量略低于系统软件容许余差的 2 倍就可以。 取样周期时间的设置在于步幅的设置。步幅越大,多孔板旋转一个步幅使操纵目标从一个平稳情况衔接到下一个平稳情况所历经的时间段越长,相对应的也要较长的取样时长。取样周期时间的设置还可以在操作系统的校准历程中开展,取样周期时间应略长而多孔板旋转一个步幅所造成的闸阀的输入输出的改变做到平稳值所必须的较长时长。 步进电机控制法德余差与步幅的设定相关。假如依照一个步幅所造成的被闲置量的较大变化量略低于静态数据误差值的标准设定步幅,则无论电动蝶阀用以平稳系统软件或是用以追随系统软件,其导出的余差都不可能超过系统软件的静态数据误差值。 因为电子计算机导出的是固定不动的小增加量,而且相匹配于每一个这种的小增加量操纵目标的变化量不得超过静态数据误差值的 2 倍。故选用步进电机控制法闸阀导出的开环增益在数据上不得超过系统软件的静态数据误差值。 由于阀门执行机构中惯性力等要素的存有,使闸阀在启闭操作过程中具有最优控制。依照传统的调节规律性闸阀每一次在健身运动不断的時间较长,最优控制的危害通常可以忽略。
在步进式操纵中,闸阀的导出做到设定量分析必须根据多个步幅才可以进行。恰好是因为每一步中最优控制项的积累危害,促使步进式操纵的反应速度比别的操纵方法慢,衔接时间长。而且精度越高响应时间变慢。图3是假设闸阀增益值为变量定义 3,继电器阶段导出 Ua 为0.01,执行器开环传递函数为 1/N(s 1),选择步幅为 0.01,取样时间为 8s,步进式操纵对企业阶跃键入的反应速度与立即回应法获得同样导出稳定值时的响应时间较为的 simulink 模拟仿真图(图3)。从下图可以看得出前面一种的调整时长约 260s,而后面的调整时长仅约 80s,二者的响应时间相距 2 倍以上。
济钢 500t pd 环状套筒规格石灰窑应用炼钢炉液化气生产制造炼铁用活力石灰粉,相匹配一定的生产效率,规定单位时间内进到石灰窑的液化气的总热值基本上维持稳定。因为液化气的发热量起伏区域比较大,必须依据生产效率和液化气的发热量及其该生产效率下企业商品的热耗测算出相应的液化气总流量。根据操纵液化气总流量来平稳入窑液化气的总热值。应用步进式控制措施,根据液化气主管电动蝶阀对液化气总流量开展调整。最先依据技术必须将液化气总流量误差的规定值设置为 ±100m3/h,液化气总流量在这个区域内起伏对石灰粉的培烧加工工艺并没有显著危害。随后依照 2.1 和 2.2 上述的办法将步幅值设定为多孔板总开启度的 3%;将取样周期时间设定为 5s。
以上方式 执行后,发动机燃烧室和循环系统汽体环境温度的起伏基本上清除,石灰粉品质明显增强。
除此之外,步进式控制法还运用于济钢(马)中板厂热处理炉空然配制自动控制系统和济钢第三炼铁厂 4 号连铸污水处理压力自动控制系统等操作系统中。 步进电机控制法是依据对调节目标的测定结论来决策闸阀启闭方位的,并且每一次启闭的偏移量是确定的,不用依靠数学分析模型来明确操纵规律性。适用数学分析模型不适合推算出或数学分析模型不确定性的场所。该制作方法操纵电动蝶阀,因为每一次的偏移量小,造成的偏差也小。可以使目标运作稳定,静态数据偏差还可以操纵在一个较小的范畴。与选用对输出量立即回应的控制措施对比响应时间比较慢,不适感用以对响应时间规定较高的场所。但对一般的工业生产全过程来讲,其响应时间已经充足。
电动蝶阀通常做为控制系统的一个构成部分,被用于对空气的总流量或工作压力开展调整。可是电动蝶阀的插入和导出相互关系难以用一个精确的模型设计来叙述。这不但是因为闸阀频率特性的最优控制,而其因为穿过闸阀汽体的数据流量和闸阀前后左右的压力降相互之间危害无法测算。以流量监控为例子,当闸阀前后左右工作压力固定不动时总流量仅与闸阀的开启度相关,但在大部分情形下,当闸阀的阀位转变时,闸阀前后左右工作压力也会随着转变,这就时总流量增益值的测算十分困难。实际上,因为闸阀前后左右的负担在振荡要素的效果下也会出现起伏进而造成总流量的转变,穿过闸阀汽体的用户流量与闸阀的开启度不会有一一对应的关联。因为数学分析模型的不确定性,立即以多孔板的开启度做为控制自变量不可以有效地达到系統的规定,乃至将会致使安全事故的产生。随后虽然闸阀的开启度与总流量或压力降中间的分析关联不容易获得,可是依靠检测仪表却可以便捷地对闸阀在某一开度下的总流量或压力降开展精确测量。
对于气动阀门的导出易精确测量不适合估算的特性,步进式操纵不可以直接对输进数据信号开展回应,反而是分多个固定不动的步幅,使键入数据信号一步一步地靠近设定量分析。在多孔板旋转一个步幅以后都对阀体的总流量或压力降开展一次精确测量,操纵电子计算机依据精确测量值和额定值较为的结论,明确下一步多孔板旋转的方位,直到精确测量值与额定值的误差低于要求偏差时才行。 步进式操纵的编程设计不涉及到数学分析模型的研究和求得,因此相对性非常简单,一般用plc梯形图就可以完成。编程设计框架图见图1。在编程设计中必须设置2个主要参数,及步幅和取样周期时间。这两个主要参数对自动控制系统的精密度和响应时间危害比较大,设置时要充分考虑对系统精度和响应时间的规定。
电动执行器可简化为由继电器阶段和开环传递函数两部份组合而成的自动控制系统,如下图2所显示。这一自动控制系统是以工作电压数据信号 Us(即 I/V 变换后的数据信号)为键入,部位反应数据信号 Uf 为导出。只需 |e|>h,交流伺服电机便会获得尺寸为 Ua 的配电工作电压。这时的前向开环传递函数为:
式中,m为 |e|>h 逐渐的时时刻刻,n为 |e|>h 完毕的时时刻刻。
对式(1)开展拉氏反转换,可以获得部位反应数据信号 Uf,即多孔板部位的变化趋势为:
当步幅比较大,一个步幅所历经的時间较长时,式中的最优控制项 e-(t-m) 和 e-(t-n) 对响应时间的干扰较小。相反最优控制要素对响应时间的危害比较大。不难看出,步幅越小,精度越高,但响应时间变慢。步幅的设置可以在操作系统的校准历程中依据对调节目标的测定结论开展,多孔板旋转一个步幅所造成的总流量或压力降的较大变化量略低于系统软件容许余差的 2 倍就可以。 取样周期时间的设置在于步幅的设置。步幅越大,多孔板旋转一个步幅使操纵目标从一个平稳情况衔接到下一个平稳情况所历经的时间段越长,相对应的也要较长的取样时长。取样周期时间的设置还可以在操作系统的校准历程中开展,取样周期时间应略长而多孔板旋转一个步幅所造成的闸阀的输入输出的改变做到平稳值所必须的较长时长。 步进电机控制法德余差与步幅的设定相关。假如依照一个步幅所造成的被闲置量的较大变化量略低于静态数据误差值的标准设定步幅,则无论电动蝶阀用以平稳系统软件或是用以追随系统软件,其导出的余差都不可能超过系统软件的静态数据误差值。 因为电子计算机导出的是固定不动的小增加量,而且相匹配于每一个这种的小增加量操纵目标的变化量不得超过静态数据误差值的 2 倍。故选用步进电机控制法闸阀导出的开环增益在数据上不得超过系统软件的静态数据误差值。 由于阀门执行机构中惯性力等要素的存有,使闸阀在启闭操作过程中具有最优控制。依照传统的调节规律性闸阀每一次在健身运动不断的時间较长,最优控制的危害通常可以忽略。
在步进式操纵中,闸阀的导出做到设定量分析必须根据多个步幅才可以进行。恰好是因为每一步中最优控制项的积累危害,促使步进式操纵的反应速度比别的操纵方法慢,衔接时间长。而且精度越高响应时间变慢。图3是假设闸阀增益值为变量定义 3,继电器阶段导出 Ua 为0.01,执行器开环传递函数为 1/N(s 1),选择步幅为 0.01,取样时间为 8s,步进式操纵对企业阶跃键入的反应速度与立即回应法获得同样导出稳定值时的响应时间较为的 simulink 模拟仿真图(图3)。从下图可以看得出前面一种的调整时长约 260s,而后面的调整时长仅约 80s,二者的响应时间相距 2 倍以上。
济钢 500t pd 环状套筒规格石灰窑应用炼钢炉液化气生产制造炼铁用活力石灰粉,相匹配一定的生产效率,规定单位时间内进到石灰窑的液化气的总热值基本上维持稳定。因为液化气的发热量起伏区域比较大,必须依据生产效率和液化气的发热量及其该生产效率下企业商品的热耗测算出相应的液化气总流量。根据操纵液化气总流量来平稳入窑液化气的总热值。应用步进式控制措施,根据液化气主管电动蝶阀对液化气总流量开展调整。最先依据技术必须将液化气总流量误差的规定值设置为 ±100m3/h,液化气总流量在这个区域内起伏对石灰粉的培烧加工工艺并没有显著危害。随后依照 2.1 和 2.2 上述的办法将步幅值设定为多孔板总开启度的 3%;将取样周期时间设定为 5s。
以上方式 执行后,发动机燃烧室和循环系统汽体环境温度的起伏基本上清除,石灰粉品质明显增强。
除此之外,步进式控制法还运用于济钢(马)中板厂热处理炉空然配制自动控制系统和济钢第三炼铁厂 4 号连铸污水处理压力自动控制系统等操作系统中。 步进电机控制法是依据对调节目标的测定结论来决策闸阀启闭方位的,并且每一次启闭的偏移量是确定的,不用依靠数学分析模型来明确操纵规律性。适用数学分析模型不适合推算出或数学分析模型不确定性的场所。该制作方法操纵电动蝶阀,因为每一次的偏移量小,造成的偏差也小。可以使目标运作稳定,静态数据偏差还可以操纵在一个较小的范畴。与选用对输出量立即回应的控制措施对比响应时间比较慢,不适感用以对响应时间规定较高的场所。但对一般的工业生产全过程来讲,其响应时间已经充足。
咨询需求
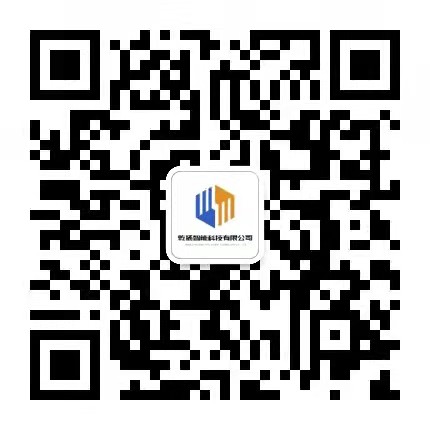